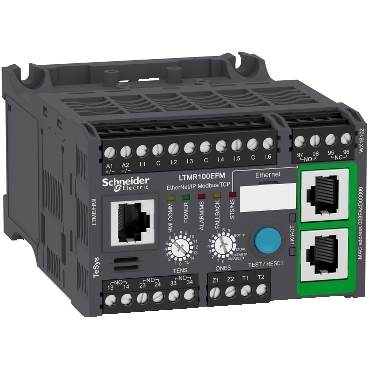
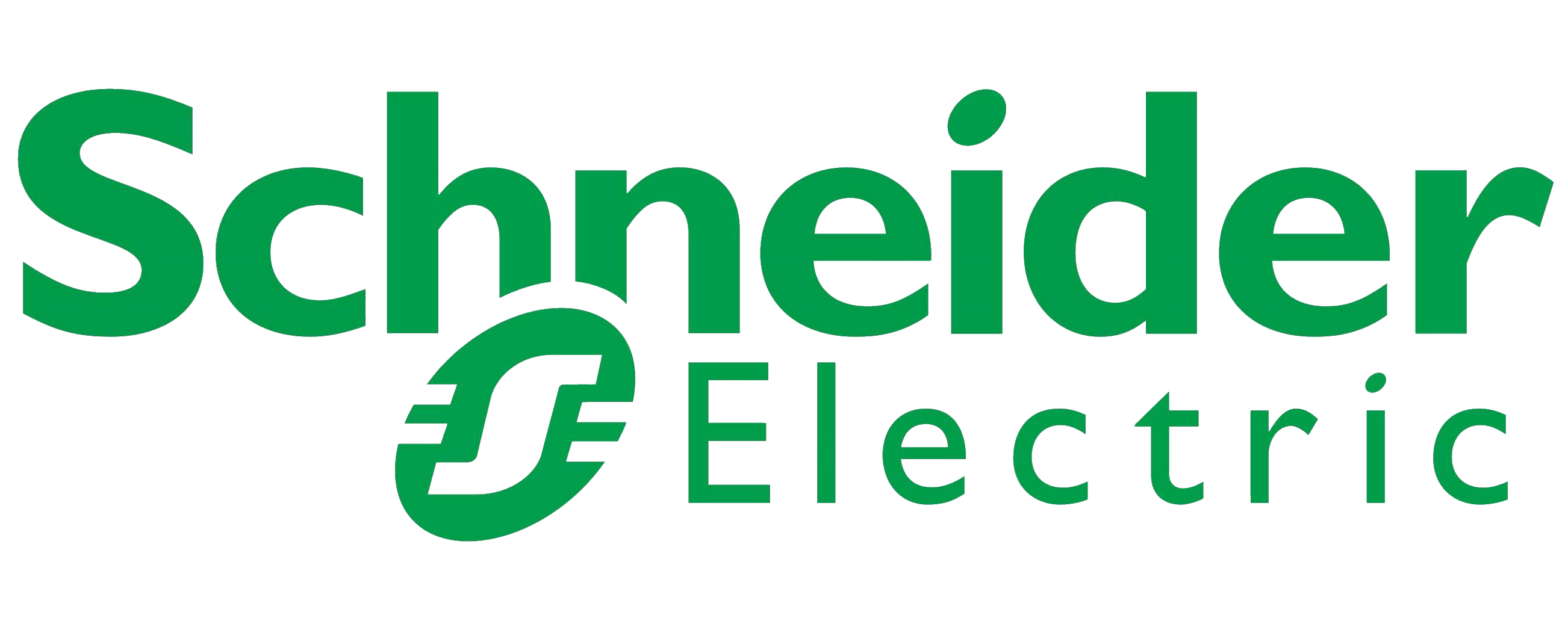
Motor Management, TeSys T, motor controller, Ethernet/IP, Modbus/TCP, 6 inputs, 3 outputs, 5 to 100A, 100 to 240 VAC
Mfr. Part No.:
LTMR100EFM
APT Stock No.:
SE-LTMR100EFM
Brand:
Schneider Electric
Back Order
Need more stock?
Contact us for Est. Lead TimeSubtotal (1 unit)**
GHS 13,120.60
(Exc. VAT)
GHS 15,994.01
(Inc. VAT)
Available For Order
* Delivery dates may change based on your quantity and address.
Shipping & Policy
Payment Methods:
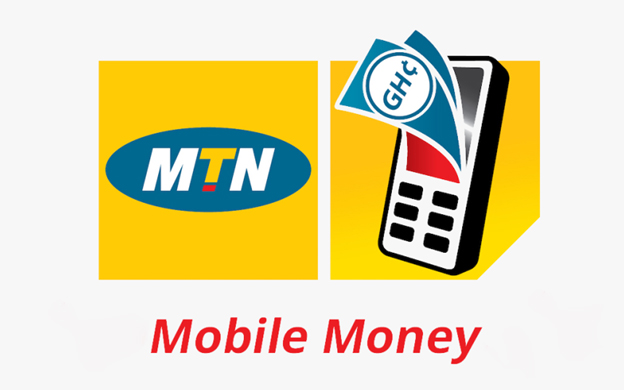
Shipping Cost:
Contact the supplier about freight and estimated delivery time.
Secure payments:
Every payment you make on aptghana.com is protected by the platform.
Return policy
Enjoy peace of mind with our 7-day return policy for used items, provided they are returned in their original packaging.
Description
TeSys T is a motor management system that provides full motor monitoring, control, and protection when used with short circuit protection and a contactor. TeSys T manages most critical processes while reducing downtime and increasing productivity. TeSys T is a flexible system that integrates seamlessly into your automation system through five major communication protocols. TeSys T predicts what will happen in the process, as it accurately monitors current, voltage, and power over a wide range. This controller is the central component in the motor management system. The module manages the basic functions of the motor management system. It manages the measurement of 3 phase current via integral current transformers from 0.4 to 100 A or up to 810 A by external current transformers. It also measures ground current with internal or external ground sensors, motor temperature and the inputs and outputs for the various motor control modes, detected fault management and other functions. Ethernet/IP and Modbus/TCP protocol is used by this controller. Ethernet TCP/IP communication is used. This module has 6 discrete logic inputs, 3 relay logic outputs and a relay output for detected fault signaling overload relay. The current range of this controller is 5 to 100 amperes. 120 to 240 VAC is used to power this controller. Controller has the following certifications: UL, CSA NOM, ATEX, BV, EAC, RINA, LROS, DNV, ABS, GL, KERI, RMRoS, C-Tick and CCC.
Shipping & Policy
Payment Methods:
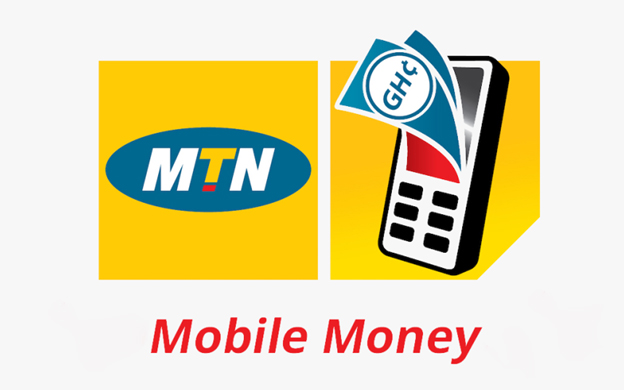
Shipping Cost:
Contact the supplier about freight and estimated delivery time.
Secure payments:
Every payment you make on aptghana.com is protected by the platform.
Return policy
Enjoy peace of mind with our 7-day return policy for used items, provided they are returned in their original packaging.
Compatible products
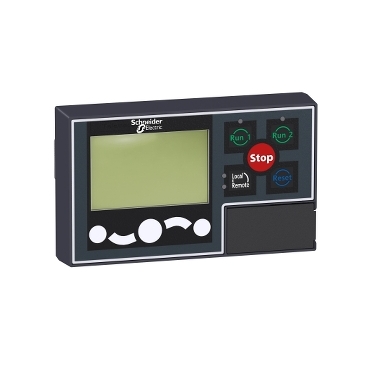
Accessories (4)
Specifications
Main | |
---|---|
Range | TeSys |
product name | TeSys T |
Device short name | LTMR |
Product or component type | Motor controller |
Device application | Equipment monitoring and control |
Measurement current | 5…100 A |
[Us] rated supply voltage | 100...240 V AC 50/60 Hz |
Current consumption | 8...62.8 mA |
Supply voltage limits | 93.5…264 V AC |
Communication port protocol | Modbus TCP/EtherNet/IP |
Bus type | Ethernet IEEE 802.3 interface, addressing 0...159, transmission rate 10...100 Mbit/s, RJ45 with 2 shielded twisted pairs |
Complementary | |
---|---|
[Ui] rated insulation voltage | 690 V conforming to EN/IEC 60947-1 690 V conforming to CSA C22.2 No 14 690 V conforming to UL 508 |
[Uimp] rated impulse withstand voltage | 4 kV supply, inputs and outputs conforming to EN/IEC 60947-4-1 6 kV current or voltage measurement circuit conforming to EN/IEC 60947-4-1 0.8 kV communication circuit conforming to EN/IEC 60947-4-1 |
Short-circuit withstand | 100 kA conforming to EN/IEC 60947-4-1 |
Associated fuse rating | 4 A gG for output 0.5 A gG for control circuit |
Protection type | Reverse polarity protection Overload Phase unbalance Overload (long time) Thermal protection Power factor variation Thermal overload protection Locked rotor Earth-leakage protection Load fluctuation Phase failure |
Network and machine diagnosis type | Waiting time after overload tripping Motor control command recording Trip context information Phase fault and earth fault trip counters Starting current and time Trip history information Fault recording Event recording Remaining operating time before overload tripping Running hours counter/operating time |
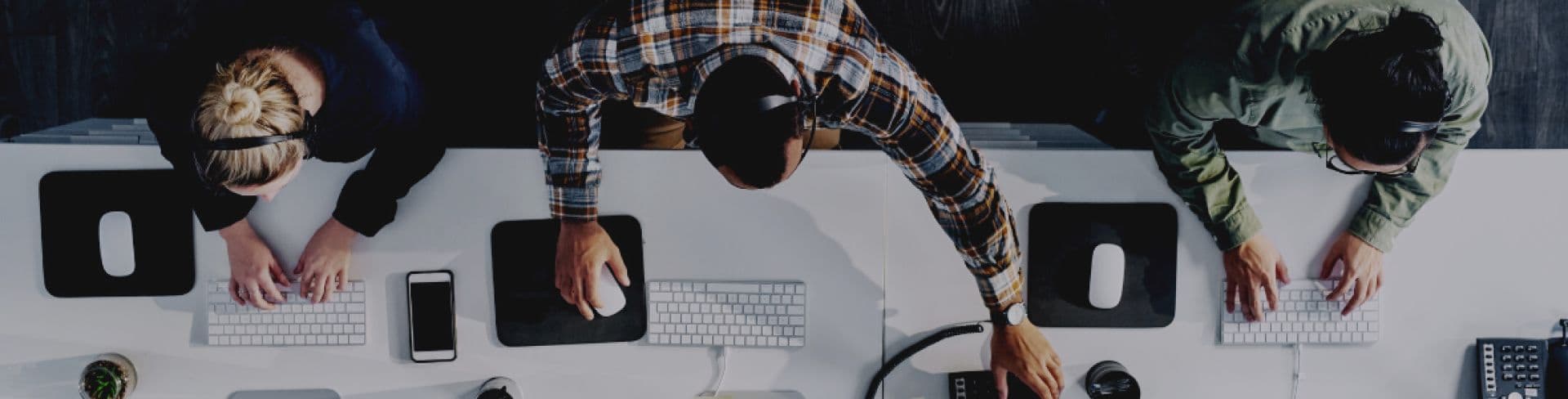
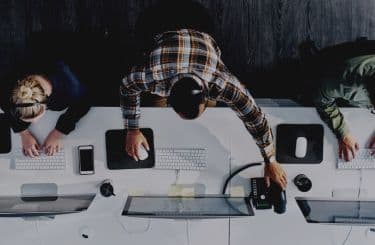